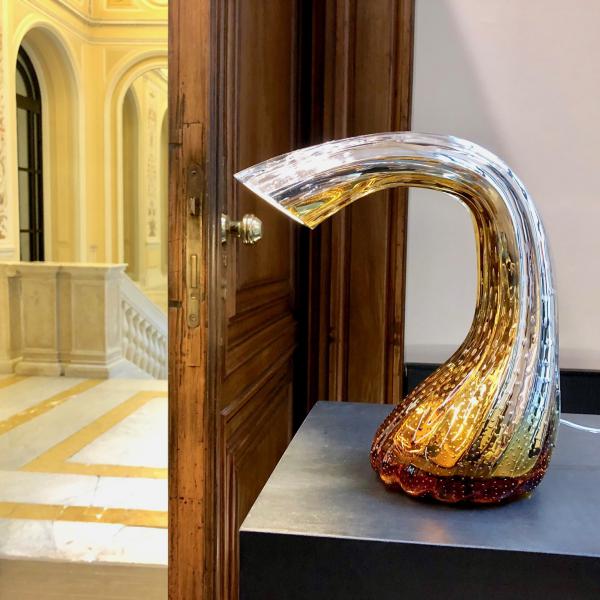
Frozen Movement
The glassblowers are accustomed to making a single design in series, turning them out as if on a production line. Thanks to this routine they can offer a consistently high quality, so that the thickness of the glass is correct to the millimetre. With me it’s a different matter: as soon as we have a good model we go and do something different. We are constantly trying new things and often this goes wrong. At the end of the day we have a mountain of shattered glass and occasionally a couple of new designs. This design is called the Liquid Light, a lamp that is made in one go from a large, drawn-out blob of glass: a frozen movement. The lamp is made without a mould, even without equipment; the perfect coordination of hands and mouth is all it takes. It is always difficult to bend the blob of glass while simultaneously blowing it into the form of a desk lamp.
The initial design was transparent, but later versions were coloured as well. Once the correct form is achieved it is cooled down further in the annealing oven, still attached to the blowpipe, until fully solidified. After at least 24 hours of slow cooling the lamp can be tapped off the pontil, ground smooth, holes drilled and polished. Bulbs, wires and transformers are fitted at the studio in Arnhem.
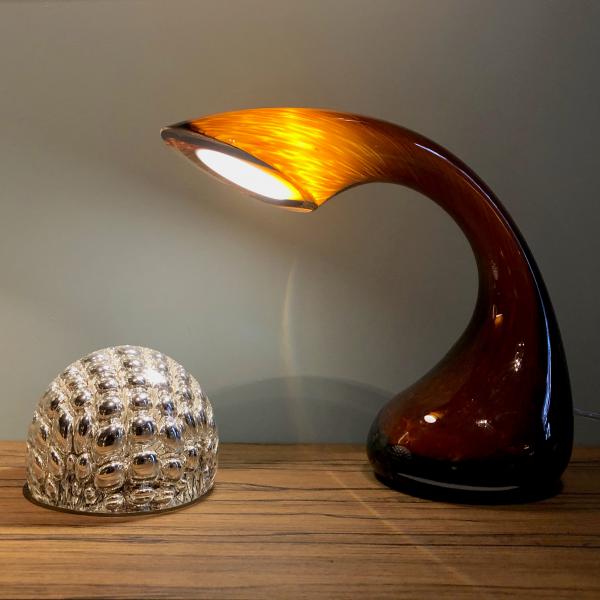
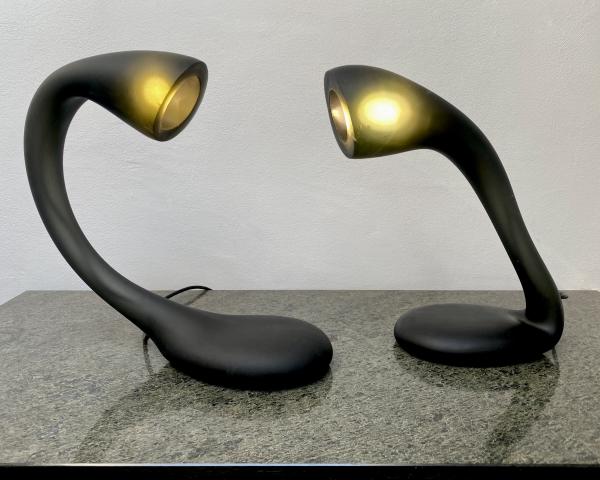
All around the world
I like to work with glassblowers all over the world. Every team has a unique signature, reflecting in different works of art. In Kitengela, Kenya, we work with recycled window glass, resulting in robust lamps. In Czeck Republic, we work with the finest glass, resulting in crystal glass lamps. Every lamp is unique!
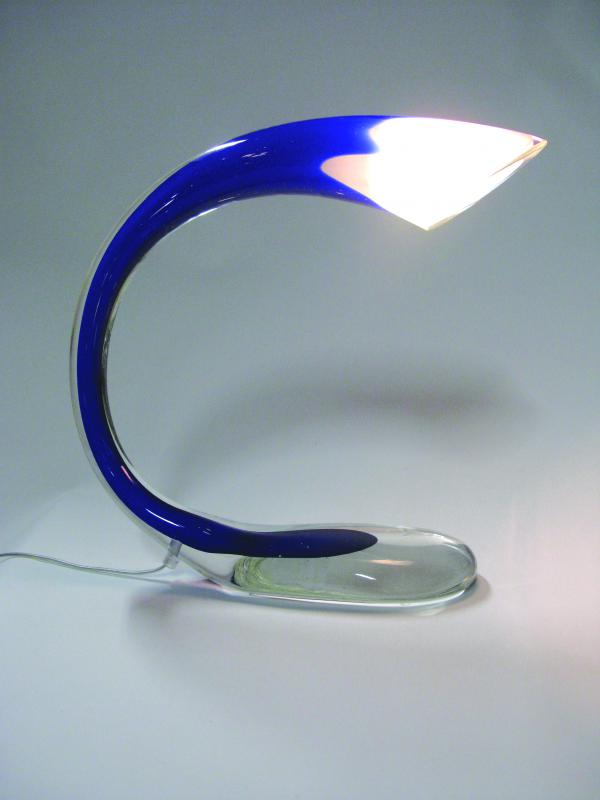
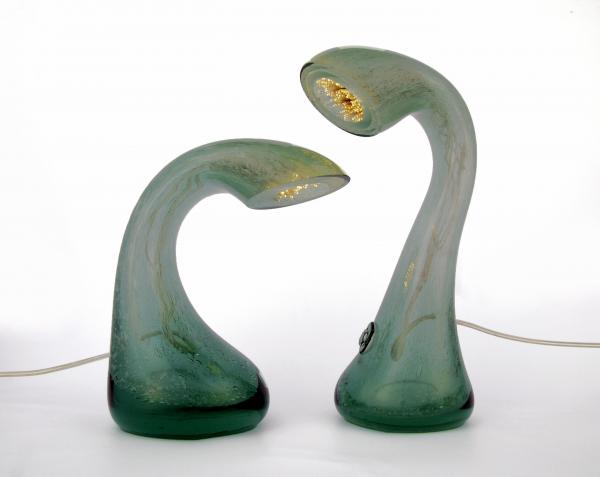
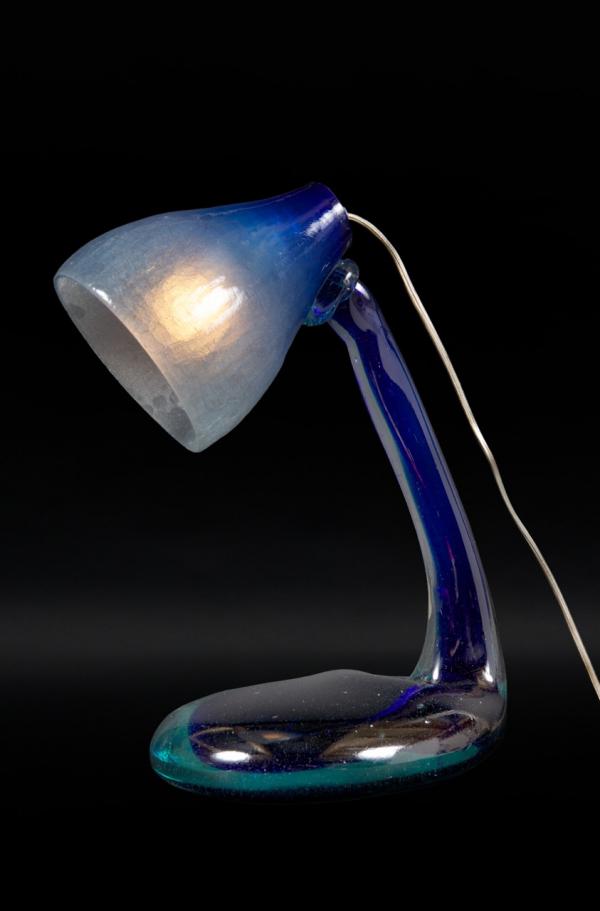
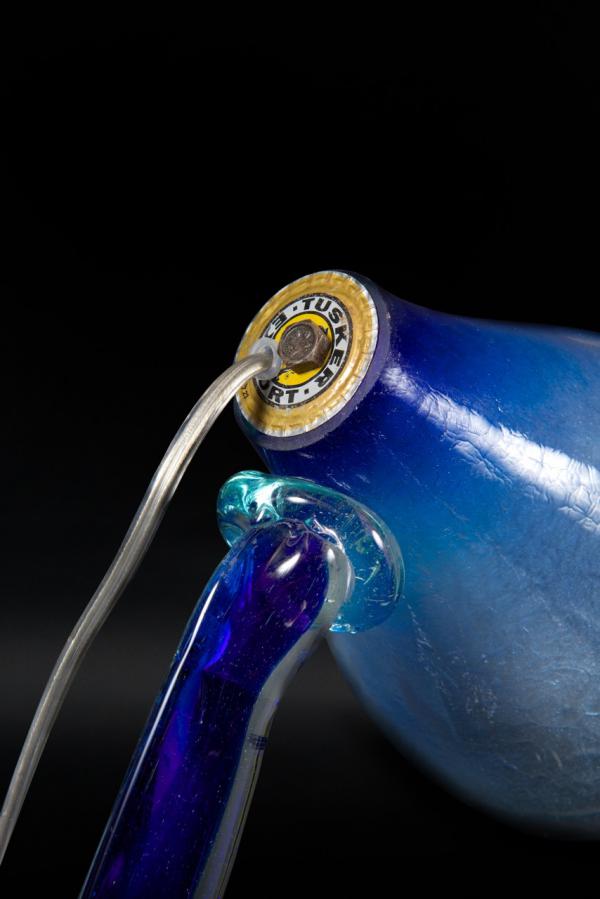